Printed circuit boards are necessities in electronics of all types. They’ve been used for several decades, and engineers continue to make them smaller and more powerful. Because of the complexity of PCBs and the factors that go into producing them, they are available in a variety of price points.
What Are The Factors That Affect The Cost Of PCB?
PCBs might be small, but they are mighty. To do their jobs efficiently and effectively, they have several factors that affect their costs.
Type of PCB Material
PCBs are made out of different materials like fiberglass, polymer inks, and solder. The conductive layers are usually made of copper, gold, or silver. These materials can affect the way the board reacts to heat. PCBs need to have thermal reliability and temperature reliability. They also need to have other mechanical properties that affect the performance of the board and the device it powers. When PCBs need to have higher frequencies, the boards need to be made of higher-grade materials – like gold or silver – than the standard copper boards.
PCB Size and the Number of Layers
PCBs that run high-tech electronics tend to have several layers. Of course, boards that are composed of more than one layer, or one with components on two sides will cost more than a single-layer board. PCBs need several components, which is why they need so many layers stacked upon each other.
When boards are bigger, they cost more than the smaller ones. The space that the components consume increases the cost of the PCBs. The price increases not just because the PCBs are bigger; this is because bigger boards and boards with several layers take more time to manufacture.
Size of Board Holes 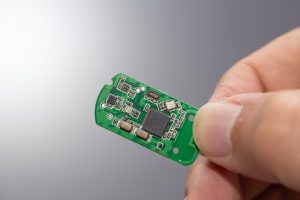
PCBs also have holes that can increase the cost of production. These holes require precise drilling, especially when boards are thick or compact. The holes help the PCBs fit together or send messages through different components.
Cost of Labor
Producing PCBs is a costly endeavor because skilled professionals do the work. They need to use automated machinery that is designed specifically for PCB manufacturing. Labor costs affect the price of producing a PCB, and no one wants to have inexperienced workers create these important components for complex electronic devices. It is better to pay a fair wage for employees to build high-quality boards the first time, then paying to have them made twice by mediocre employees.
Expected Turnaround Time
Some manufacturers are building PCBs with a quick, turn-key turn around time. When manufacturers are asked to produce PCBs quickly, they will charge more money. Often, manufacturers have to put other orders on hold to get a quick turnaround on another order. The increased price will cover the expense of putting other orders on hold.
If you are looking for a way to reduce your costs, place your order early. This gives your manufacturer time to complete the order without forcing them to pay overtime or higher shipping costs to get parts.
Quantity of PCB in the Order
PCBs often have a lower cost if they are ordered in bulk. Once a prototype is made, it is easy to duplicate them. Building the prototype is expensive, which is why small orders cost more per piece than a bulk order does. Many companies will discount bulk orders, so do not be afraid to request a lower price.
If you ever want to know what could be slowing down your pcb prototyping check out this article here.
Technology Used in PCBs
The technology that manufacturers use to produce the PCBs will also affect the price. Manufacturers use one or two different production methods to make PCBs: surface-mount technology or through-hole technology. Surface-mount technology is the least expensive of the two because it uses more automation, which requires less manpower and lower employee costs.
Other Custom Specifications
PCB costs are often determined by custom specifications. If you are looking to save money on PCB manufacturing, it is best to design a board that has few customizations. Try to use component designs from previous boards.
Packaging Costs
Shipping fragile electronics components can be expensive. Some PCBs need to be packaged with their electrical parts connected, and these types of projects often need delicate packaging materials, which adds to the cost of the manufacturing.
How Much Does A PCB Cost?
In general, the cost to produce a PCB will cost between $10 and $50 per board. The actual price will be determined by the manufacturer and could be higher or lower based on the components, size, and type of material used. Sometimes, the smaller boards cost more because they require more labor hours to get components working properly, especially if the board has to power something like a smartphone or other small, complicated device.
What To Consider When Looking For A PCB Manufacturer?
Before you choose your PCB manufacturer, you should look at more than the price. There are several important factors to consider, including what type of PCBs they specialize in and the quality of the products they make. You don’t want to hire a PCB manufacturer to make your smartphone boards if they specialize in making boards for high-tech washing machines. Once you find a PCB manufacturer who meets your needs, then you should see if they produce high-quality boards for an affordable price. Share as much information as possible about your product so the PCB manufacturer can give you a realistic quote.
You might find that hiring a PCB manufacturer in the USA, which is close to your business, will reduce the cost, simply because of reduced shipping costs. But, you might also find an overseas PCB manufacturer that offers a lower price. Weigh all factors relating to your budget before you make a decision.
In conclusion, the cost of manufacturing PCBs is affected by several factors. It is important that you choose a company that meets your technology needs and also meets your budget. If you are looking for a way to reduce costs, try to design a PCB with a few unique parts from a local manufacturer with a lot of time to complete the project.