When just starting out in the prototyping business, it can be difficult to know where to begin. As far as PCBs (printed circuit boards) go, there’s everything from single layer to double layer and beyond—but what does it all mean? With so many PCB types on the market, how can you possibly know what’s best for your business or product?
If you’re someone who’s interested in PCBs and how they are made—whether you’re new to the industry or are simply still at an early point in your career and want to learn how to make your products more efficient with different boards—this is for you. Continue reading to learn about the different types of PCBs to aid in your decision-making on which to ultimately go with for your company.
What Is a Printed Circuit Board?
First, let’s review what PCBs are so you can get a stronger sense of why they’re important. They are actually used in most electronics! They’re boards that serve both as the wiring area for surface-mounted or socketed components, and as physical support pieces. They are usually made of a composite epoxy, fiberglass, or from another kind of composite material.
That’s why they are so crucial—from computers and TVs to digital cameras, radios, and even cell phones, you’d be somewhat hard-pressed to find a device you use on a daily basis that doesn’t utilize the power of a good PCB. Industries that heavily rely on them include medical technology, industrial machinery, lighting, automotive, and aerospace, to name a few.
What Are the Different Types of PCBs?
The main reason we’re glad you’re reading this post is that it’s critical you know that certain types of PCBs are best used in certain projects. If you’re looking to manufacture PCBs or an electronic product, working with a PCB manufacturer who is familiar with these boards may be the best way to set yourself up for success. That way, you will be well set up to avoid errors, wasted money, lost time, and other potential headaches.
Discover some of the most common types below!
Single Layer PCBs
This PCB is made of one, single layer of a base substrate. One side of the base’s material is coated with a thin metal plating, such as copper, after which point a protective solder mask is typically applied. At that, you would go through a final silkscreen stage to mark out all the board’s elements.
This type of PCB is easy to design and manufacture because single-layered ones only have their components and circuits soldered onto one side. Due to their popularity, they can also be purchased at a low-cost—especially for those high-volume orders.
Double Layer PCBs
These are also known as double-sided PCBs and have a base material with a layer of conductive metal—again, often being copper—applied to both sides of their board. Holes are drilled to allow one side’s circuits to connect with those on the other side.
Double-sided PCBs are commonly used in applications that require a more intermediate level of circuit complexity, for instance, power supplies, industrial controls, instrumentation, LED lighting, HVAC systems, amplifiers, automotive dashboards, and vending machines, too.
Multi-layer PCBs
The multi-layer kinds consist of a series of at least three double-layered PCBs. The boards are bound together by a specialized glue and then sandwiched between bits of insulation in order to ensure any excess heat doesn’t melt the components. Multi-layer PCBs come in various sizes that range from boards as small as four layers or as large as twelve.
Since there are many layers with this type of PCB, designers can create thicker, more complex designs suitable for a wide range of complicated electrical needs. File servers, GPS technology, data storage, weather analysis, satellite systems, and medical equipment are all applications that benefit from multi-layer PCBs.
Rigid PCBs
Rigid PCBs are when the boards are made up of a solid substrate that keeps them from twisting around. A computer motherboard is one of the most popular examples of a rigid kind of PCB and this category likely makes up the largest number of manufactured PCBs.
It’s a multilayer type constructed in a way that allocates electricity from the power supply and at the same time allows adequate communication between all the various parts of the computer, for instance, the GPU, CPU, and RAM. They come in handy when there’s a need for the board itself to be set up in a particular shape and stay that way throughout the device’s entire lifespan. Rigid PCBs can be a simple single-layer up to a more complex, ten-layer multi-layer PCB.
Flexible PCBs
Unlike their rigid, non-moving counterparts like fiberglass, flexible PCBs are made up of materials that have more give, such as plastic. Similar to rigid types, flexible PCBs also come in single, double, or multilayer formats. They tend to cost more, though, since they need to be printed on a more flexible material.
Regardless, the flexible kinds offer several advantages over rigids. Because they are flexible, they can be wrapped around corners and folded over edges. Manufacturers also often realize cost savings when using these since a single flexible board can be used to cover areas that may have otherwise taken multiple rigid PCBs.
They can also be used in areas that could be subject to some environmental hazards, so you may find them being built waterproof, corrosion-resistant, shockproof, and resistant to high-temperatures—options traditional, rigid PCBs might not have.
High-Frequency PCBs 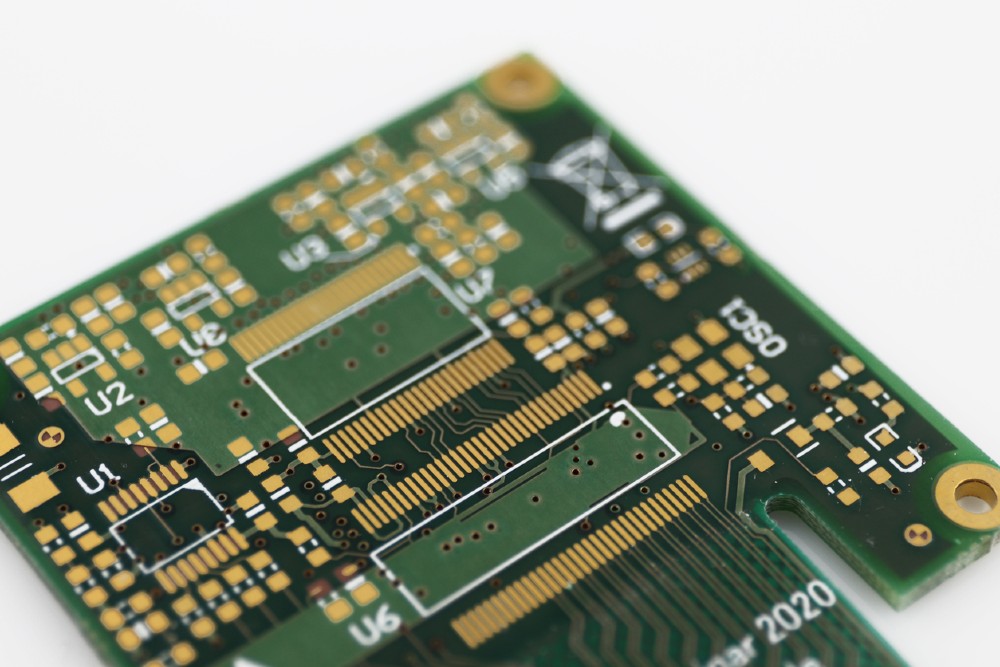
Rather than a kind of PCB construction, high-frequency PCBs actually refer to a more general element of PCB design. They are circuit boards made to transmit signals greater than one gigahertz and include polyphenylene oxide (PPO) resin, FR4-grade glass-reinforced epoxy laminate, and Teflon. This may be an expensive option due to its smaller, more stable dielectric constant, along with smaller amounts of dielectric loss, and low water-absorbing quality, overall.
High-frequency PCBs are designed in a way that prevents loss of digital signal integrity by guarding against the disruption of the harmonics that make up a digital signal. When choosing a high-frequency PCB board, you will need to consider things like dielectric loss (DF), thermal expansion, water absorption, and other resistances (ie. heat, impact, and hazardous chemicals).
Aluminum Backed PCBs
Instead of the standard fiberglass used in many PCB board types, aluminum-backed PCBs typically utilize an aluminum substrate. The aluminum backing gets lined with a thermal-insulating material designed with a low thermal resistance—which means less heat gets transferred to the backing from the insulating material. After the insulation is applied, it receives a circuit layer of copper.
Aluminum-backed PCBs have many benefits that are not seen in PCBs that have a fiberglass backing, such as lower cost, being more environmentally friendly, is great when it comes to dissipating heat away from critical circuit board components, and is very durable.
These advantages make aluminum-based PCBs a fantastic choice for applications that need large outputs of power within tight tolerances. Examples include traffic lights, power supplies, automotive lighting, motor controllers, and high-current circuits.
Time to Get Serious About Your PCB Manufacturing Game
By knowing all your options before you begin a PCB project, you’ll already be ahead of the game. And, when you partner with a knowledgeable PCB manufacturer, you’re proactively making the choice to help you stand out from your competitors!